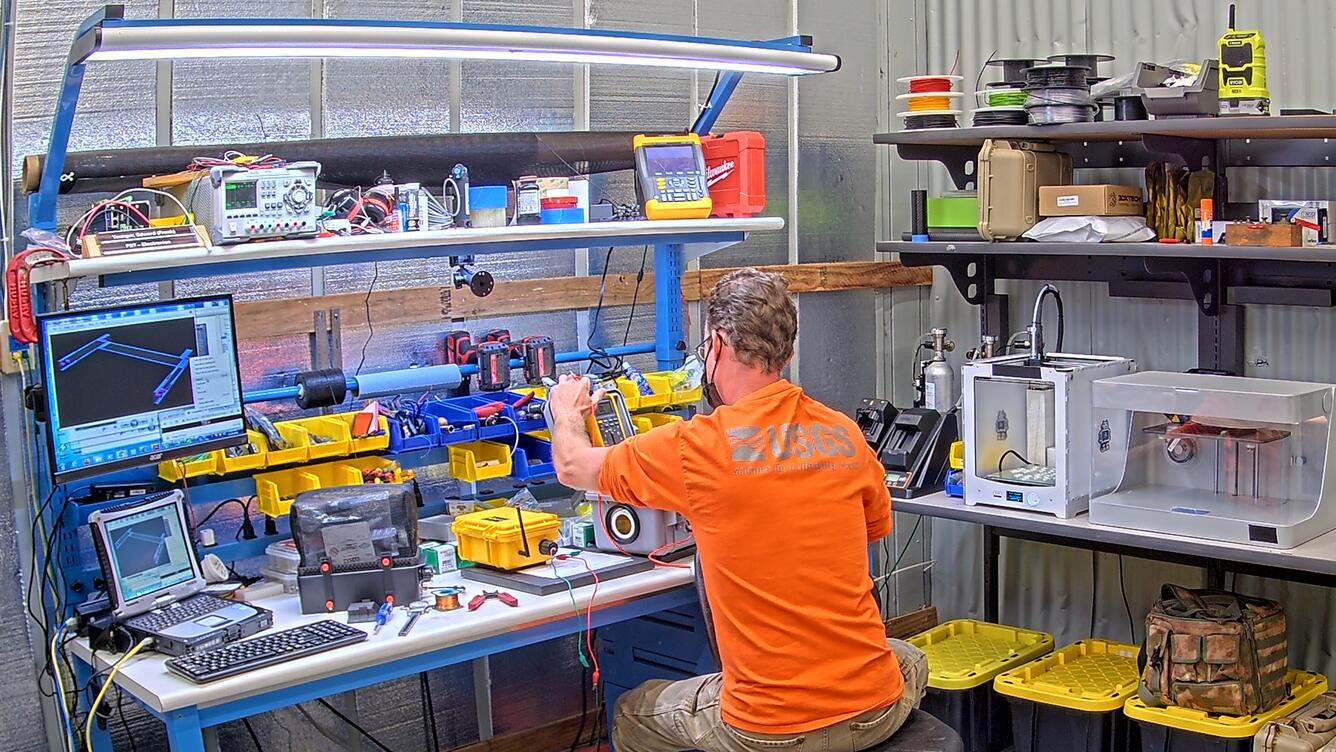
(BIVN) – Kīlauea continues to erupt lava at the summit caldera within Hawaiʻi Volcanoes National Park, and its USGS Volcano Alert level is at WATCH.
In this week’s Volcano Watch article, Hawaiian Volcano Observatory Technician Frank Younger writes about innovation – and 3D application – when monitoring the active volcano:
The electronics workshop at the USGS Hawaiian Volcano Observatory (HVO) buzzes with creative activity. It’s like Santa Claus’ workshop—for volcano science. Workbenches line the walls of the room, cluttered with things in the making: pliers, wires, and bottles of glue; voltmeters, calipers, and microchips, too.
At one bench, a worker is hunkered, soldering a rainbow splay of wires into a cable harness. Nearby, another fine-tunes a glowing waveform on an oscilloscope. Across the room, another hurriedly puts the finishing touches on a volcano-proof camera—one of the latest models.
The electronics shop is well-lit, ventilated, and fully networked. There’s constant motion—people and equipment flow through doors on each end. A small radio plays Jingle Bells, while someone runs a shop vacuum.
Here, technical problems are wrestled, new ideas are developed, and informal education is shared.
When the workday is done, the staff closes up, and the room grows quiet—almost. At one end of the darkened shop, there is a restless stirring: a three-dimensional (3D) printer zigzags rhythmically on its midnight program. It’s building carbon fiber drone parts, destined to fly over Kīlauea to measure volcanic gas emissions that cause volcanic air pollution (vog) downwind.
Over the past five years, HVO’s use of 3D printing has grown. It has evolved into a technique that enables custom production and high-performance innovation.
This technique has allowed HVO to realize several advantages of digital fabrication: shortened supply chains, nimble design iterations, and on-demand production.
A new idea moves forward in the design process using computer aided drafting (CAD) software. A 3D CAD model is created using engineering, drafting, and design proficiencies. The 3D model is readily tweaked, shared, and documented as part of the digital workflow.
Slicing software is used to convert a 3D model into a sequence of thin, stacked layers for 3D printing. Algorithms are used to tweak many 3D printing parameters—to optimize infill density, strength to weight, cost, and printing time.
Parts are constructed in 3D printing by depositing layer after layer of material. This type of additive manufacturing opens many design possibilities, such as low-density infill, embedded hardware, and composite reinforcement.
HVO uses two 3D printing techniques depending on the part being constructed, what it will be made of, and how it will be used.
The fused filament fabrication (FFF) process is used to 3D print parts from starch-based bioplastic. Applications have included terrain models, petrology sample holders, templates, and mounting brackets.
With the FFF technique, the 3D printer uses an extrusion nozzle on a travelling print head. Plastic filament is melted and deposited in a small bead as the print head traverses a flat plane. As the extruded material cools and solidifies, the print head rises and deposits the next layer.
To make functional parts that meet higher performance demands, HVO uses a more advanced 3D printing process: continuous fiber fabrication (CFF). Advanced composite materials—carbon fiber, Kevlar, fiberglass, and nylon—are used to achieve higher strength, durability, and dimensional tolerances.
With the CFF technique, a second printhead nozzle weaves long strands of carbon fiber into layers of extruded nylon. The reinforced composite parts can achieve strength comparable to solid aluminum, at a fraction of the weight.
Many new designs have been enabled by CFF: from airborne drone payloads, where strength-to-weight ratio is a primary consideration; to submerged crater lake instruments, where heat- and chemical-resistance are crucial.
These techniques have been used to make more than 430 unique designs at HVO over the past 5 years! Multiple versions, customization, and testing are enabled by this design/production cycle. Small quantities of each design—from one to ten parts—are efficiently printed in-house. Larger quantities are scaled-up using commercial services.
Recently, HVO has explored 3D printed metal parts. Metal powder is used as the raw material in selective laser melting (SLM). HVO has tested aluminum alloy printed parts as an alternative to traditional machining.
Like elves in Santa’s workshop, HVO technicians practice their art; they fuse software and filament to print a new part. An invention is born of necessity. At HVO, the mother of all necessity is monitoring Hawaii’s six active volcanoes.
"use" - Google News
December 12, 2021 at 09:51AM
https://ift.tt/31X4mBu
VOLCANO WATCH: HVO Makes Use Of 3D Technology - Big Island Video News
"use" - Google News
https://ift.tt/2P05tHQ
https://ift.tt/2YCP29R
Bagikan Berita Ini
0 Response to "VOLCANO WATCH: HVO Makes Use Of 3D Technology - Big Island Video News"
Post a Comment